The Critical Role of O-Rings in Perforating Guns
The Critical Role of O-Rings in Perforating Guns In the high-stakes oil and gas extraction world, every piece of equipment plays a vital role in ensuring safety and efficiency. O-rings stand out as unsung heroes among the many components that make up downhole tools. These tiny, unassuming rubber rings play a critical role in the functioning of perforating guns, an essential tool used in the industry.
What Seals Are in Perforating Guns?
Perforating guns are specialized tools for creating holes in well casing and surrounding rock formations to access hydrocarbon reserves. These guns operate under extreme pressure and temperature conditions, making it essential to prevent any leaks or damage. Various seals are integrated into the design, with o-rings being a fundamental type of seal.
O-rings are positioned strategically to prevent the leakage of wellbore fluids into the gun's sensitive electronics and explosive charges.
Are Seals Critical in Perforating Guns?
Yes. Seals, particularly o-rings, are critical in perforating guns' functioning. Any failure in the sealing system could lead to uncontrolled release of wellbore fluids into the gun:
- Damaging the electronics and shaped charges in the gun.
- Downtime to pull and replace the gun during a stage.
O-rings are a barrier between the harsh downhole environment and the gun's delicate internal components. They ensure that the explosive charges fire precisely when and where intended, maintaining the integrity of the wellbore and safeguarding the equipment. Without these seals, the risk of malfunction or compromised safety would be significantly higher.
Which O-Ring Materials Are Best for Perforating Guns?
Given the challenging conditions that perforating guns operate in, choosing o-ring material is paramount. The material must withstand extreme pressures, temperatures, and exposure to oil and gas fluids without losing its sealing properties. Common materials used for O-rings in perforating guns include:
Nitrile (NBR): Nitrile O-rings are known for resisting oil and hydrocarbon-based fluids, making them popular in the oil and gas industry.
Fluoroelastomer (FKM / VitonĀ®): These O-rings have exceptional chemical resistance and can handle various temperatures, making them suitable for harsh downhole environments.
Hydrogenated Nitrile (HNBR / HSN): HNBR O-rings combine the benefits of NBR and Viton, offering excellent resistance to temperature, oil, and chemicals.
Perfluoroelastomer (FFKM): FFKM O-rings are the top choice for extreme conditions, with exceptional resistance to high temperatures and aggressive chemicals.
O-rings play a critical role in successfully operating perforating guns in the oil and gas industry. These small but essential components act as the last line of defense, ensuring the safety and efficiency of wellbore operations. Choosing the correct o-ring material is vital to withstand the harsh downhole conditions and maintain the integrity of the equipment. Understanding the importance of these seals highlights the meticulous engineering and precision required in the oil and gas sector.
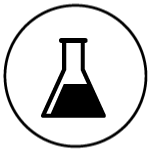
Material Selection