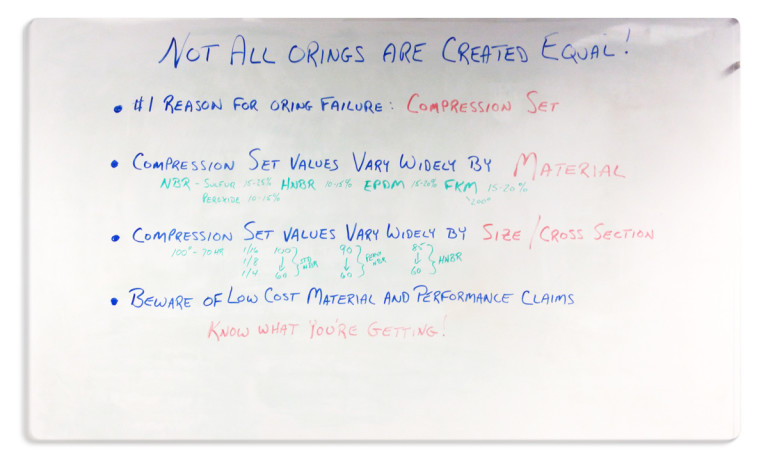
Click on the image to open in a New Tab.
Video Transcript

I will start by saying not all o-rings are created equal; different materials, different hardness’s, different curing processes, they’re not just round, they’re not just squishy and just to fill in a hole. Having said that many of you also know a lot of the basics when it comes to o-rings, but one of the things that I want to focus on today is what Parker Hannifin states is the number one cause for o-ring failure and that is compression set.
Compression set is a term that’s used for one of those physical properties that gets measured with every batch of material that gets produced by reputable o-ring manufacturers. Which is maybe clue number one. If you’re buying o-rings from a manufacturer that does not test every batch and every lot and has full traceability- that’s a red flag.
Let’s go on the premise that you’re working with people that do have full batch and lot control of every material that they produce. Tensile strength, elongation, specific gravity, TR10 values; these are all different physical properties that get measured. Compression set is one that, in my experience, [I will validate what Parker’s telling us] is probably the most important of all of them. If you don’t know what compression set is – in simplest form – it’s taking o-ring material squishing it between platens, applying pressure to squeeze at 25%, then baking it in an oven for a prescribed period. Taking it out. Undoing the platen, pull out the material and measure how much did it come back.
Now in a perfect world, it comes back all the way.
If it comes back all the way, it is taking no compression set. Also, factor in that when you design o-rings for seals you are utilizing a squeeze rate that will vary from 10%, 15%, to 20%. So, in the scenario where you have an o-ring that takes a compression set and it doesn’t come back 10%, 20%, 30% – what does that do to that design squeeze that you’ve put in there? So now similar to other variables in your design now, in essence, you have another form of tolerance stack-up.
Compression Set Varies Widely by: MATERIAL

So, let’s dive a little bit more into compression set. Compression set values vary widely by material. You use different materials for different applications. From NBRs for a lot of hydraulic applications [oil/petroleum uses in the like]. You use HNBR for lot of the same things, but when you get involved in higher temperatures or different types of fluids some compatibility issues. You use EPM, again for different applications often for ozone resistance external uses for brakes in some of those applications. FKM is used often for chemical compatibility and for high-temperature applications. Probably the four most common o-ring materials in the industrial market. Yes, there’s silicone, AFLAS, Neoprene, and others, but these are the four common.
Within these four common materials is a variance in the amount of compression set they just inherently take. Start with NBR. One thing to note about NBR is how it’s processed. There is a difference between a standard sulfur cure – which the world has known for decades – and a peroxide cure material. A peroxide cure material is a step up from the sulfur cure and one of the reasons for that, [you can see in the illustration here] is the compression set. Under standard hundred degrees C testing for 70 hours, you can expect a good sulfur cure to still have 15% to 25% compression set. Peroxide cure material you’re going to reduce that to 10% to 15%. Significant Improvement for a lot of face seals, for both static as well as dynamic applications.
You go to an HNBR which is considered an upgrade in the NBR family, and you’ll see very similar compression set characteristics of the peroxide cure. If compression set is all that we’re dealing with peroxide cure might be an alternative because there’s also a premium on price to go to the HNBR.
Another reason to go with the HNBR would be for higher temps and for other application concerns. Look at EPDM. Again, EPDM, something very similar to the sulfur cured – 15% to 20% compression set on EPDM material. FKM which gets tested at 200 degrees, so you’re not exactly comparing the same thing, but because of the higher temperature material is often tested at 200° C – you’re looking at 15% to 20% compression set. Now I want to point out that these compression set figures are also going to vary on what and how the methods are being used to test it. Slabs, buttons, dog bones – often when you’re just testing material, it’s not done with the actual o-ring. Which brings us then to the next set. When you’re looking at compression set values by o-ring, you’re going to get some wide variables as well.

Taking an o-ring material that has been molded into a shape, gone through all its curing processes and everything like that, you’re going to get variance. If nothing else do to sheer size alone. A very thin small cross-sectioned o-ring to a big fat o-ring. What are those values going to differ? You are going to see significant differences from the o-ring to just the material. At a hundred degrees for 70 hours a standard NBR 1/16th cross-section can take a 100% set. The fatter or thicker cross-sections take a 60% set.
You go to a peroxide cure, the thicker cross-sections not quite as much difference, but when you get to those thin cross sections, there’s a lot of applications out there that use the small cross-section, 90%. That 10 points can make a difference of sealing and not sealing. HNBR again a little bit better improvement. 85 to 60. 85 being the thin cross-section.
Beware of Low Cost Material & Performance Claims.

So, wide variances when you’re looking at physical properties and when you’re looking at compression set from your suppliers, understand what are you are looking at? Am I looking at raw materials, slabs, buttons, dog bones, or am I looking at actual o-rings? What are those figures and those values that you want to be able to measure to – size and cross-section do matter. Where I’m going with this – beware of low-cost materials. Not all o-rings are created equal. There are differences and low-cost materials often times will impact your compression set values. Know what you’re getting.