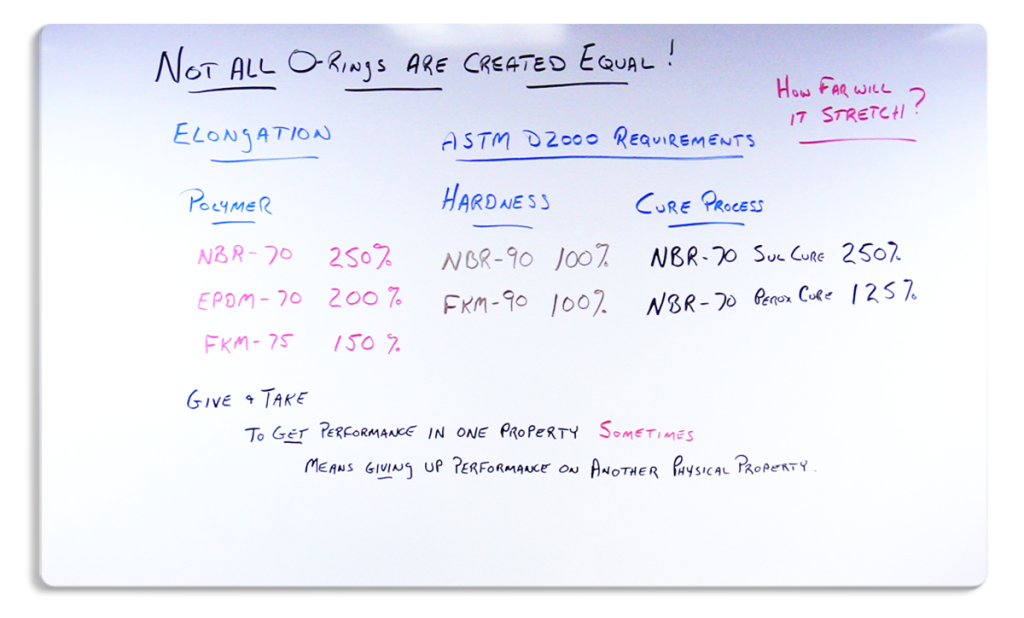
Click on the image to open in a New Tab.
Video Transcript
Welcome to our next installment of how all o-rings are not created equal. Today we are going to talk about elongation and to start us off we’re going to use the trusty Parker handbook to give their definition and then go from there.
Parker defines elongation, as it pertains to o-rings: as an increase in the length expressed numerically as a percent of initial length. It is generally reported as ultimate elongation and further, like tensile strength, elongation is used throughout the industry as a quality assurance measure on production batches of elastomer materials.*
Okay, what’s all that really saying?
Elongation comes down to how far can my o-rings stretch?
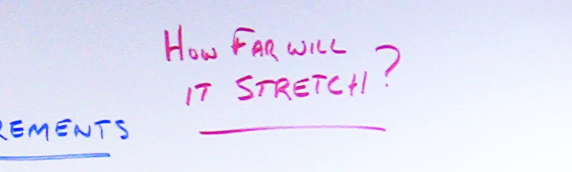
What we need to know when looking at how far an o-ring can stretch is:
- How far do you need it to stretch?
- What are the other variables that go into selecting o-ring materials and the like?
The primary reason that’s important is especially the smaller the o-ring gets, there are applications where you have to be able to stretch it over a fitting, over some type of a ledge to get to the groove that you ultimately need to be able to get to.
Always consider the elongation when it comes to installation. With that, elongation gets measured by ASTM requirements in our physical properties. We talked about compression set, when we talked about tensile strength, we talked about abrasion resistance – they all fall within the ASTM D2000 requirements.
How that affects the different materials and the ratings for elongation. Let’s look at three of the most common materials that you work within the industrial marketplace. That being nitrile or NBR, FKM or fluorocarbon, and EPDM.
From a pure polymer standpoint, elongation is as the definition, a numerical number or a percentage of the original size that the o-ring will stretch.
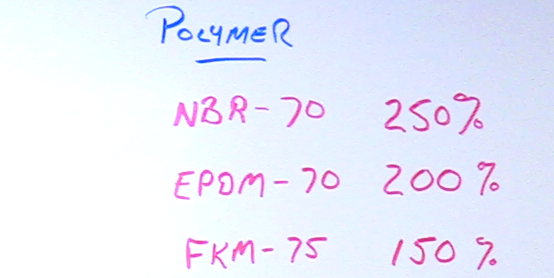
A 70 durometer NBR o-ring, typically by ASTM D2000 requirements, will stretch 250%. In practicality, most quality compounds will exceed that significantly. In the case of a 70 durometer EPDM, you’re looking at a 200% stretch. Again, most compounds, quality compounds, will exceed that by a good measure.
The closer you get down to 100%, the tighter those variances will be. With an FKM or a fluorocarbon material – 75 durometer very common – now you’re looking at only 150% stretch. So from a pure base polymer standpoint standard compounds, these are your norms.
How does the effect of hardness of the o-ring impact elongation?
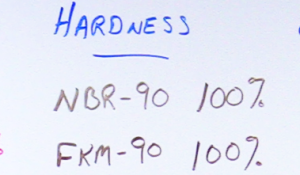
Let’s stay with the two common NBRs and FKMs. If the only thing I change is hardness and go from a 70 durometer nitrile to a 90 durometer nitrile, look what happens to my elongation. Now, my elongation is only 100%. Common applications for fittings and couplings etc. 90 durometer is a common durometer because of the properties that that hardness will give but also understand you can’t stretch it near as much as you can the 70 durometer nitrile. In the case of fkm also a significant hit from 150% for 75 durometer to only 100% for the 90 durometer.
Let’s throw one more variable in there. If compression set is a significant factor in your application, a peroxide cure o-ring is a common go to when it comes to compounds and materials.
How does the curing process within the manufacturing of the o-ring impact elongation?
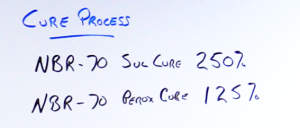
Well, a sulfur-cured 70 durometer nitrile is really the baseline that we were comparing over here at 250%. But by going to a peroxide cure material, higher compression set material, one with a little higher tensile strength – look what happens to your elongation at the same 70 durometer hardness. Drops from 250% down to 125%
Base polymer, hardness, curing process all have an impact on elongation.
One last thing I want to point out.
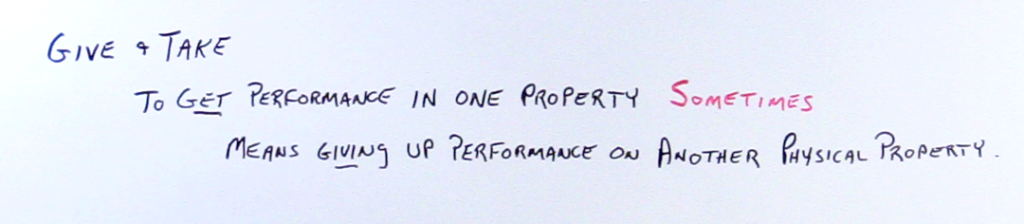
There’s some give and take as there is with most compounds and most elastomers when you’re trying to reach a particular physical property within that. Elongation just like any of the others.
To get performance in one property sometimes means giving up performance in another physical property.
You want elongation, you got to stretch this part significantly without breaking, but in order to get that based on the other criteria:
- Do I have to give up compression set?
- Do I have to give up tensile strength?
- Do I give up abrasion resistance?
- What are the give and takes?
Know the basics – elongation- how far can I stretch but what else do I need my material to do?
Again, not all o-rings are created equal!
SOURCES: *Parker Hannifin Corporation, “Parker O-Ring Handbook – ORD 5700”